- Joined
- Jun 21, 2008
- Messages
- 17,023
- Reaction score
- 47
After a discussion in a recent thread re push-fits and crimps I thought I would do a mini experiment.
Materials and method
A length of 2.5mm T&E roughly 30cm long was taken along with two lengths of 2.5mm stranded conduit cable. The twin and earth was stripped down so I had 2 equal lengths.
The cables were cut into three equal length parts and 0.75cm stripped from each end. The solid core 2.5mm was joined with a red straight crimp, crimped twice with a decent quality ratchet crimp tool using the correct die. The stranded cable was joined with a blue crimp, in the same way. Each was covered with a length of heat-shrink and it was warmed using a hot air heat gun.
The cables were then fitted with a 2 way 24A push fit connector as sold by cpc. This left the cables back to their original length with a push fit and a crimp. The cable was clamped in a bench vice and a pair of pliers was used to pull the cable to see which connector gave way first.
Results
Each cable gave way at the crimp with the push-fit holding tight. There was noticeably more force required to pull apart the crimp on the stranded cable.
It took me [an amateur, but someone who has used both methods in the past] 5 minutes to do four crimp joints with heat shrink. I fitted all four push-fits in less than 30 seconds. The cables were all prepared the same way before I started timing.
Discussion
Time is money in real life. If you can fit a push fit connector in less than 10 seconds when a crimp joint takes over a minute in a consumer unit change situation where a lot of cables need extending the time saving could be significant.
There is a lot less space needed around the cable to fit a push fit than get a pair of crimping pliers in, so more applications [eg repairing a damaged cable in the wall.
In my experiment [i have no means of measuring force] all the crimps failed with moderate pressure, none of the push-fits could be dismounted with all my bodyweight pulling against them. The bench with >100kg tools was moving and the push-fits plastic deformed but remained tight.
Conclusion
A push-fit is clearly stronger than a crimp, faster and easier fitted. In a consumer unit or any cable extension situation I can't see how it could be thought of as any less 'professional'.
Materials and method
A length of 2.5mm T&E roughly 30cm long was taken along with two lengths of 2.5mm stranded conduit cable. The twin and earth was stripped down so I had 2 equal lengths.
The cables were cut into three equal length parts and 0.75cm stripped from each end. The solid core 2.5mm was joined with a red straight crimp, crimped twice with a decent quality ratchet crimp tool using the correct die. The stranded cable was joined with a blue crimp, in the same way. Each was covered with a length of heat-shrink and it was warmed using a hot air heat gun.
The cables were then fitted with a 2 way 24A push fit connector as sold by cpc. This left the cables back to their original length with a push fit and a crimp. The cable was clamped in a bench vice and a pair of pliers was used to pull the cable to see which connector gave way first.
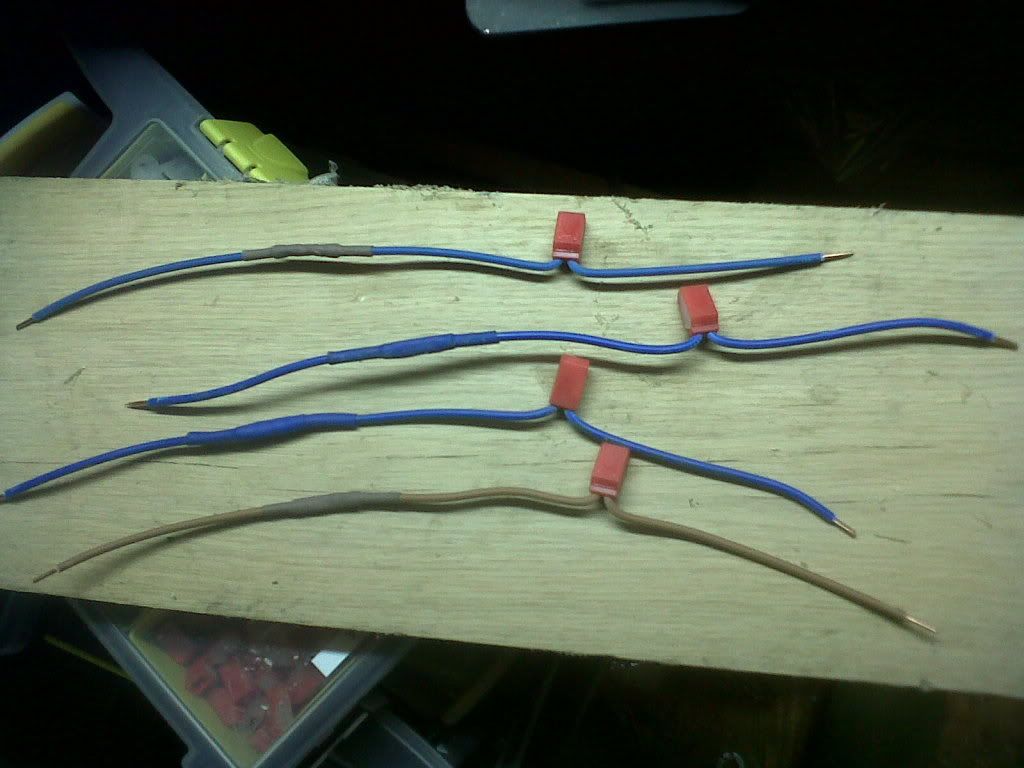
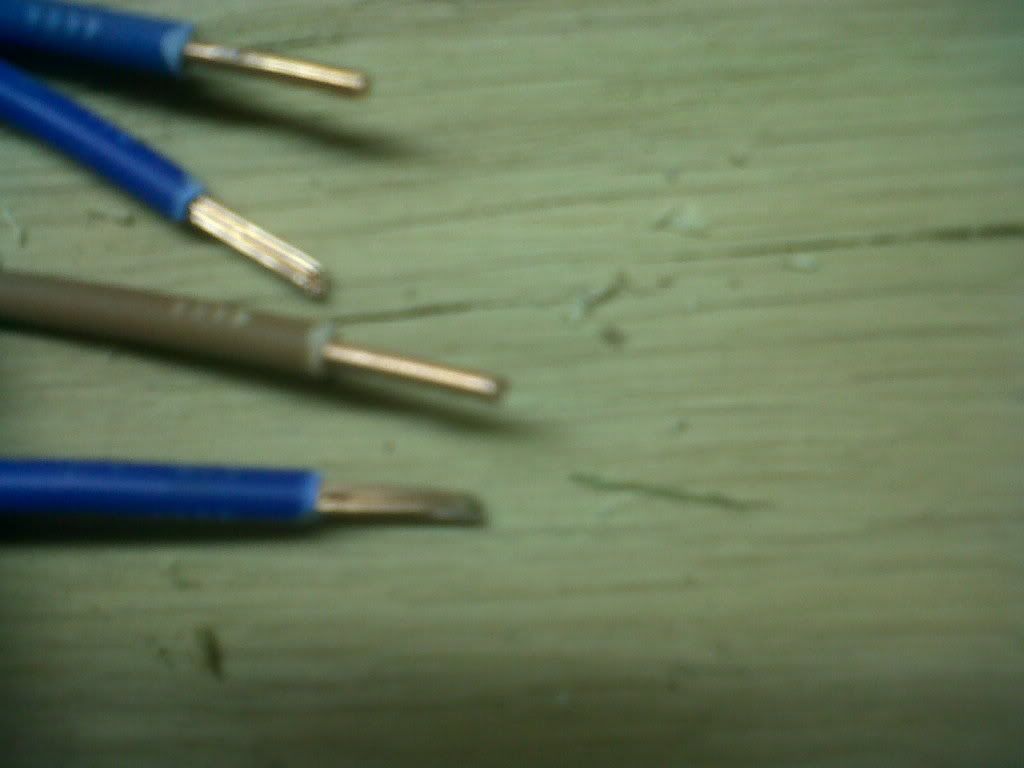
Results
Each cable gave way at the crimp with the push-fit holding tight. There was noticeably more force required to pull apart the crimp on the stranded cable.
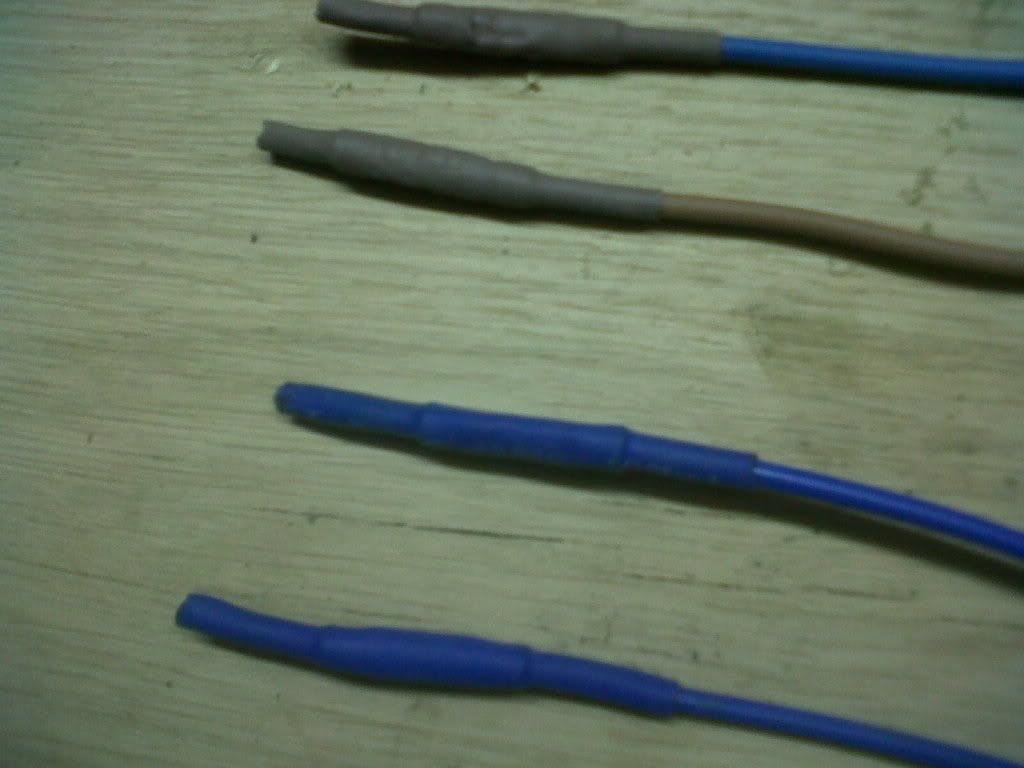
It took me [an amateur, but someone who has used both methods in the past] 5 minutes to do four crimp joints with heat shrink. I fitted all four push-fits in less than 30 seconds. The cables were all prepared the same way before I started timing.
Discussion
Time is money in real life. If you can fit a push fit connector in less than 10 seconds when a crimp joint takes over a minute in a consumer unit change situation where a lot of cables need extending the time saving could be significant.
There is a lot less space needed around the cable to fit a push fit than get a pair of crimping pliers in, so more applications [eg repairing a damaged cable in the wall.
In my experiment [i have no means of measuring force] all the crimps failed with moderate pressure, none of the push-fits could be dismounted with all my bodyweight pulling against them. The bench with >100kg tools was moving and the push-fits plastic deformed but remained tight.
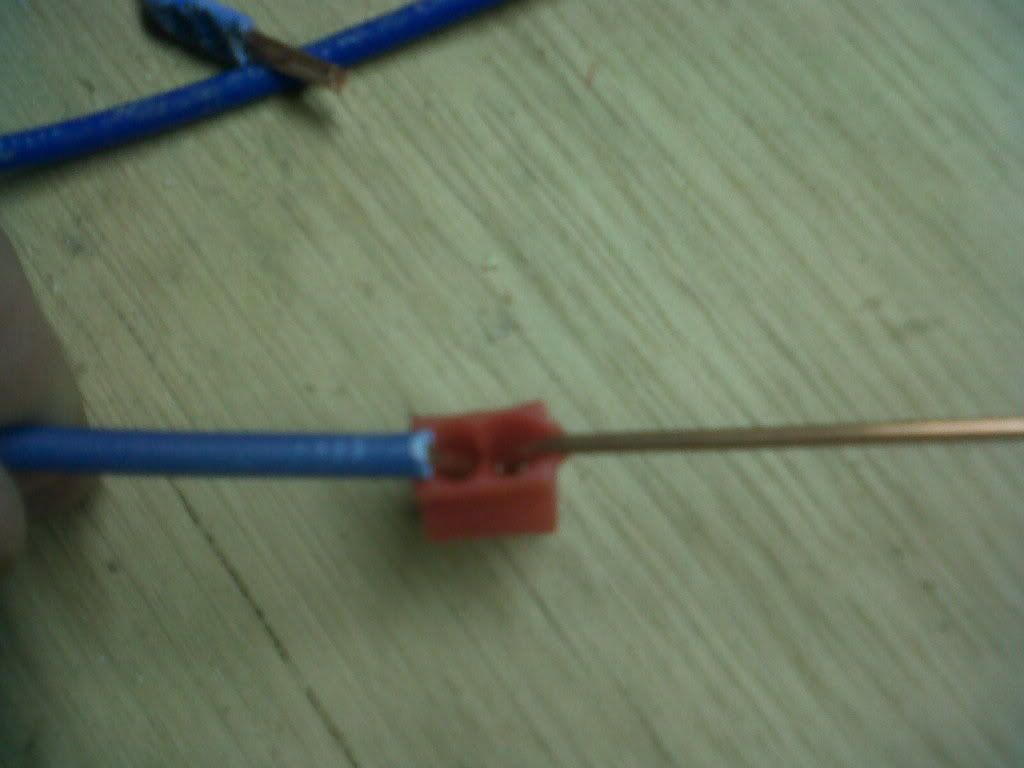
Conclusion
A push-fit is clearly stronger than a crimp, faster and easier fitted. In a consumer unit or any cable extension situation I can't see how it could be thought of as any less 'professional'.